Monarc concrete colours are designed using select local sources of aggregate, sands, cement and oxides. Concrete formulas are then engineered and blended together through a controlled process to create a beautiful concrete matrix that reveals nature's beautifully perfect colours.
Selecting a colour from Monarc’s exclusive range or working with the Monarc team to develop your own unique blend - Monarc will meet your design needs and will compliment the most discerning Material selection palettes.
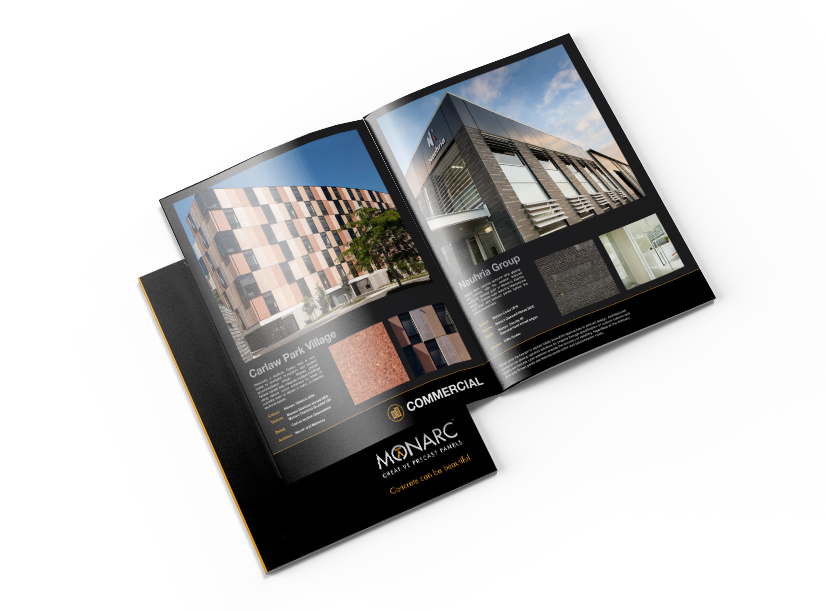
DOWNLOAD OUR BROCHURE
Gain insight into Monarc's capabilities and add the info to your products library.
Want to know how Monarc's precast concrete will work for your project?
Get in touch today and a member of the team will talk you through your options.